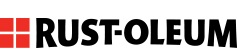
Engineering & Facilities Manager
JOB DESCRIPTION
Tremco Construction Products Group brings together Tremco CPG Inc.'s Commercial Sealants & Waterproofing and Roofing & Building Maintenance divisions; Tremco Barrier Solutions Inc.; Dryvit, Nudura and Willseal brands; Prebuck LLC; Weatherproofing Technologies, Inc.; Weatherproofing Technologies Canada and PureAir Control Services, Inc.
Altogether, Tremco CPG companies operate 21 manufacturing facilities, 6 distribution sites, and 3 R&D/technology sites, and employ more than 2,700 people across North America.
The Engineering, Facilities and Maintenance Manager is responsible for directing all engineering activities and maintaining and upgrading the Site's facilities and production equipment.
In addition, this position is responsible for maintaining/advancing a viable and visual Preventative Maintenance Program at the facility, while identifying capital requirements for the annual capital plan.
Responsibilities also include developing and assisting in value stream design and implementation of lean principles and tools within the manufacturing environment.
This includes, but is not limited to, assisting with value stream mapping, employee training, continuous improvement event facilitation, waste identification and elimination, problem solving (through the scientific method), work area and station design and layout, visual control implementation, material flow, and progress tracking and communication.
Lastly, this resource acts as a passionate advocate for a cultural change toward lean thinking throughout the organization.
ESSENTIAL DUTIES AND RESPONSIBILITIES:
- Partner with LEAN leadership in eliminating unplanned production interruptions.
- Use DAKOTA as the compliance tool to report incidents, near misses and non-conformances, and to maintain compliance with EH&S.
- Work with the maintenance crew to implement the needed preventative measures.
- Recommend design modifications to eliminate machine or system malfunctions.
- Prepare capital projects for submission to management.
Included are costs, schedule, Job Hazard Analysis (JHA), Process Hazard Analysis (PHA), and needed procedures. - Serve as lead project engineer for approved capital projects with the goal of on time and on budget completion.
- Develop and administer a viable and visual Preventative Maintenance Program that reduces downtime and improves overall reliability of production and production supporting machinery.
- Responsible for identifying capital requirements for the facility's annual capital plan and budget.
- Direct, review, and approve product design and changes consistent with MOC procedures.
- Recruit departmental employees; assign, direct, and evaluate their work; and oversee the development and maintenance of staff competence.
- Analyze annual site utility expenditure and develop plan to optimize plant efficiency to reduce costs (ISO 14001).
- Perform administrative functions such as reviewing and writing reports, approving expenditures, enforcing rules, and making decisions about the purchase of materials or services.
- Integrate the plant PHA initiative with the appropriate capital projects.
- Investigate equipment failures and difficulties to diagnose faulty operations and work with the maintenance crew to implement the needed preventative measures.
- Interface with leadership, operators, and maintenance to develop needed TPM programs.
- Support SPC, DOE's, and other Quality initiatives.
- Lead Engineer for the production processes.
- Develop facility infrastructure upgrade plan.
EDUCATION REQUIREMENT:
- B.S.
in Mechanical, Chemical or Electrical Engineering.
EXPERIENCE REQUIREMENT:
- At least 1-2 years in a supervisory role.
- 5-10 years of Facility and Process Engineering experience.
- Experience managing capital projects required.
- Experience is Engineering Management.
- PHA and "Process Safety Management" experience a positive.
OTHER SKILLS, ABILITIES, AND QUALIFICATIONS:
- Mechanical - Knowledge of machines and tools, including their designs, uses, repair, and maintenance.
- Production and Processing - Knowledge of raw materials, production processes, quality control, costs, and other techniques for maximizing the effective manufacture and distribution of goods.
- Computers and Electronics - Knowledge of circuit boards, processors, chips, electronic equipment, and computer hardware and software, including applications and programming.
- Complex Problem Solving - Identifying complex problems and reviewing related information to develop and evaluate options and implement solutions.
- Deductive Reasoning - The ability to apply general rules to specific problems to produce answers that make sense.
- Problem Sensitivity - The ability to tell when something is wrong or is likely to go wrong.
It does not involve solving the problem, only recognizing there is a problem. - People Interaction - Ability to work with diverse groups to reach consensus regarding problems, and needed changes.
PHYSICAL DEMANDS:
- Incumbent must be able to stand, walk, sit, use hands, reach, balance, talk, hear, and lift up to 50 lbs.
BENEFITS AND COMPENSATION:
- The salary range for applicants in this position generally ranges between $99,222 and $124,027.
This range is an estimate, based on potential employee qualifications, operations, needs, and other considerations permitted by law. - The Company offers a variety of benefits to its employees, including but not limited to health insurance, paid holidays, paid time off, 401(k) Savings and Trust & Plan with company match, Company Pension Plan, Performance Based Bonus/Commission, and continuing education.
All qualified applicants will receive consideration for employment without regard to their race, color, religion, sex, sexual orientation, gender identity, national origin, disability or veteran status.
Apply for this ad Online!
- Location: North Kingstown, Rhode Island
- Type: Permanent
- Industry: Accountancy
- Recruiter: Rust-Oleum
- Email: to view click here
- Posted: 2025-02-11 22:13:47 -
- View all Jobs from Rust-Oleum
More Jobs from Rust-Oleum
- Construction Products Sales Representative
- Maint Mechanic - 3rd Shift
- Machine Operator- 2nd Shift
- Technical Sales Representative - New York, NY
- Technical Sales Representative - New York, NY
- Field Operations Manager
- Technical Sales Representative - New York, NY
- Machine Builder
- Machine Operator - 3rd Shift
- Territory Sales Representative
- Production Operator
- Production Operator
- Production Operator
- Production Operator
- Packaging Operator - 3rd Shift
- Shipper/Receiver
- Production Operator
- Machine Operator- 1st Shift
- Packaging Operator - 2nd Shift
- Senior Maintenance Technician